Composite Materials R&D
Development and Fabrication
DET has considerable experience in the development, analysis and manufacture of novel composite materials. We are skilled in traditional methods of fabricating composite materials as well as the development of cutting edge manufacturing processes for composites.
Materials
Low-density-High-strength composites
High-density-High-strength composites
High-temperature composites
Reactive composites
Glass, carbon, and ceramic fiber preforms
Low-density-High-strength composites
High-density-High-strength composites
High-temperature composites
Reactive composites
Glass, carbon, and ceramic fiber preforms
Fabrication Methods
Net shape preform fabrication utilizing:
2-D braiding: planar, tubular, and complex geometries
3-D braiding: solid or hollow preforms with constant or non-constant cross-sections while
maintaining uniform fiber distribution and fiber orientation
Resin-transfer molding
Compression molding
Net shape preform fabrication utilizing:
2-D braiding: planar, tubular, and complex geometries
3-D braiding: solid or hollow preforms with constant or non-constant cross-sections while
maintaining uniform fiber distribution and fiber orientation
Resin-transfer molding
Compression molding
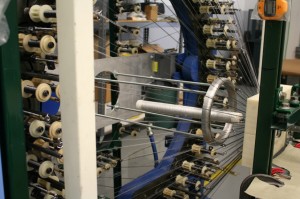
Braiding machine in use.
Applications
Defense
Aerospace
Automotive
Medical
Recreation
Defense
Aerospace
Automotive
Medical
Recreation
Process Development
Under a current SBIR Program, we are developing a novel process for producing three-dimensionally braided-fiber preforms with solid circular non-uniform cross-section for ceramic matrix composites. The process’s unique capability is the production of preforms with varying cross-sectional shapes and dimensions while maintaining constant fiber distribution and orientation throughout the preform.
Under a current SBIR Program, we are developing a novel process for producing three-dimensionally braided-fiber preforms with solid circular non-uniform cross-section for ceramic matrix composites. The process’s unique capability is the production of preforms with varying cross-sectional shapes and dimensions while maintaining constant fiber distribution and orientation throughout the preform.